SERVICE |
サービス紹介 |
---|
当社は「やり方を簡単にする」ことで、業務を改善します。
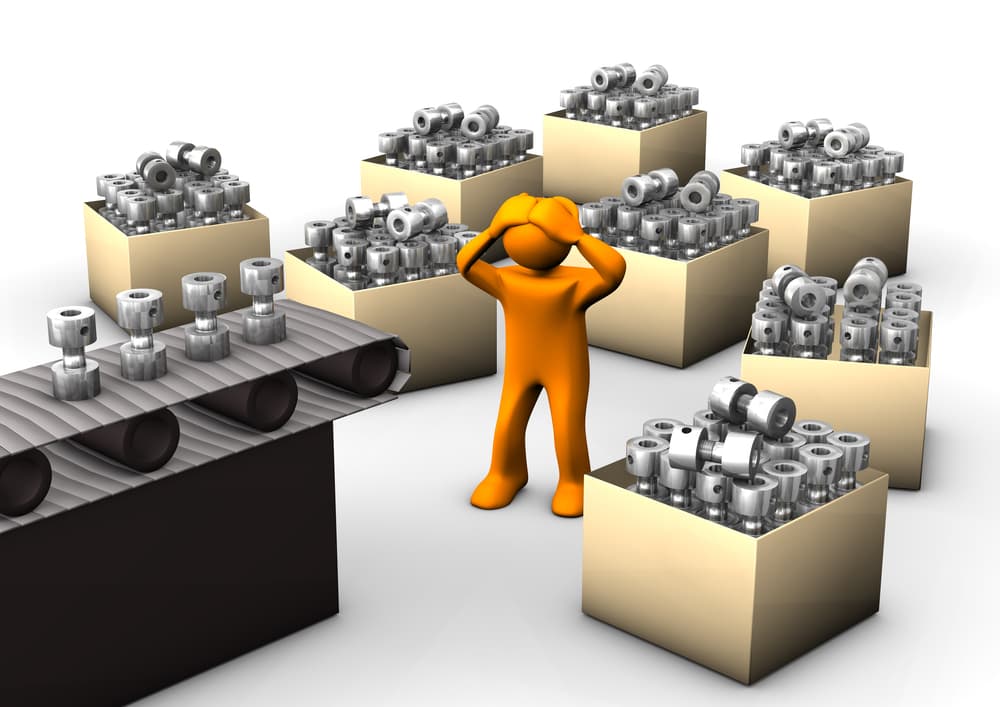
製造業向け
工期短縮・在庫削減
「在庫がたくさんあるのに出荷したい製品は在庫切れが頻発する」、「仕掛品がたくさんあるのに部品不足で製造ラインが停止することがある」、「出荷までに十分な余裕があるはずなのにいつも納期ギリギリになる」
このような生産現場では管理方法を少し変えるだけで簡単に問題を解決できます。
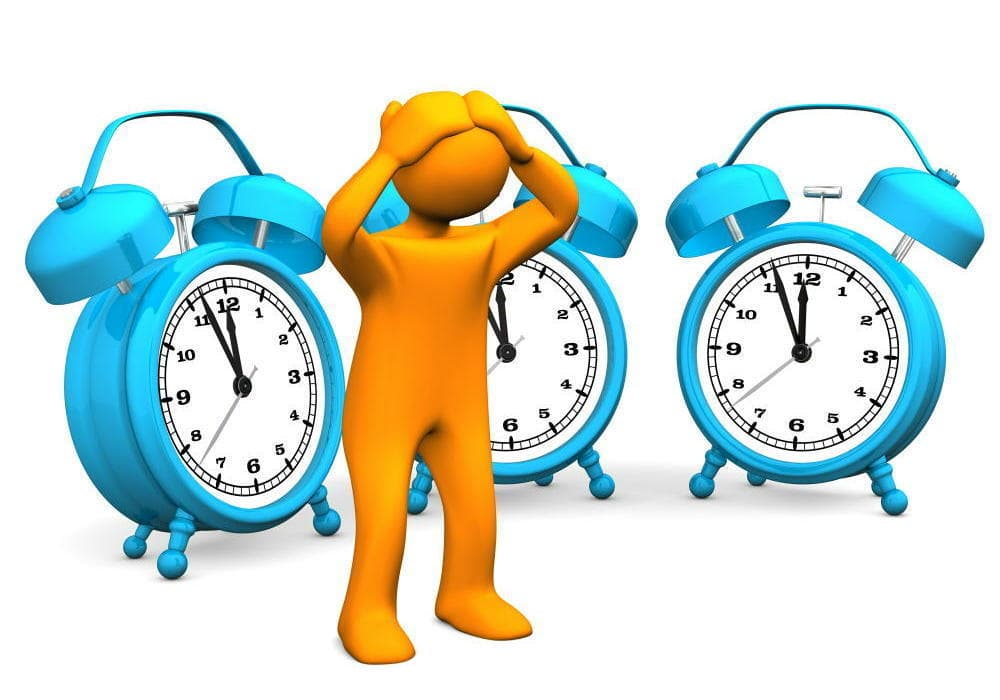
ITベンダー向け
納期遵守率向上
開発プロジェクトは予想できないことが多いため納期遅延が起こりがちです。しかし、プロジェクト管理のやり方を少し変えるだけで納期遵守率が飛躍的に向上します。
「タスクの優先順位の明確化」「安全余裕の組み込み方」「進捗報告のやり方」を変えるだけで納期遅延は激減します。
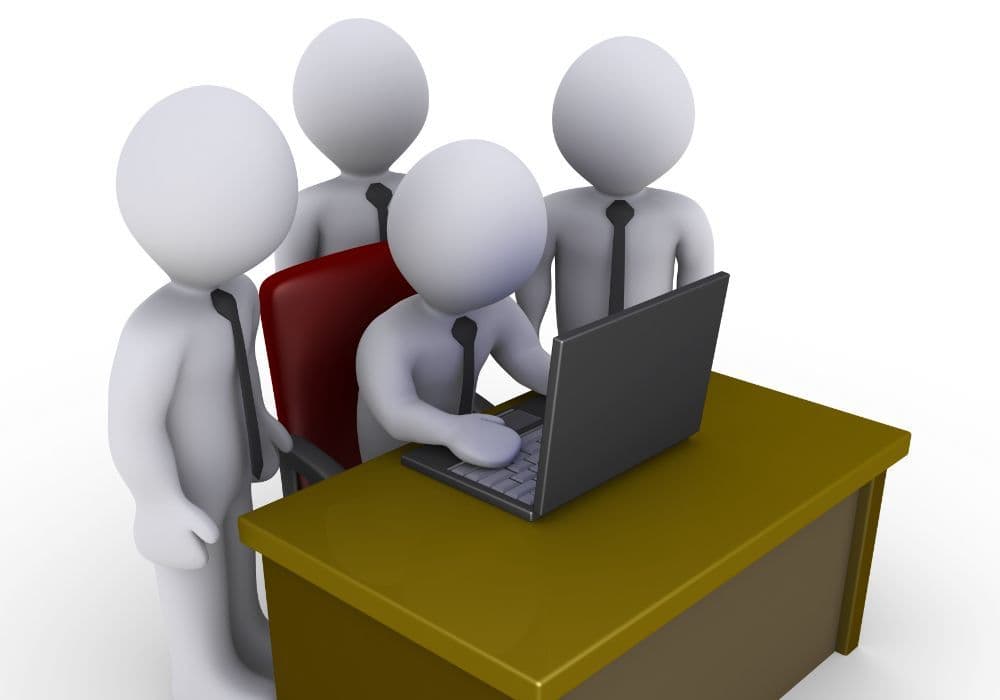
全業種向け
補助金獲得支援
景気回復のために国は様々な補助金を用意しています。製品・サービスを開発する企業にとって使いやすく、金額が大きい補助金として「ものづくり補助金」と「事業再構築補助金」があります。
弊社では補助金申請支援(採択までの支援)ではなく、交付申請や実績報告も支援しています。採択後は何も支援してもらえずお困りの方のお手伝いもしています。
料金表はこちらをクリック
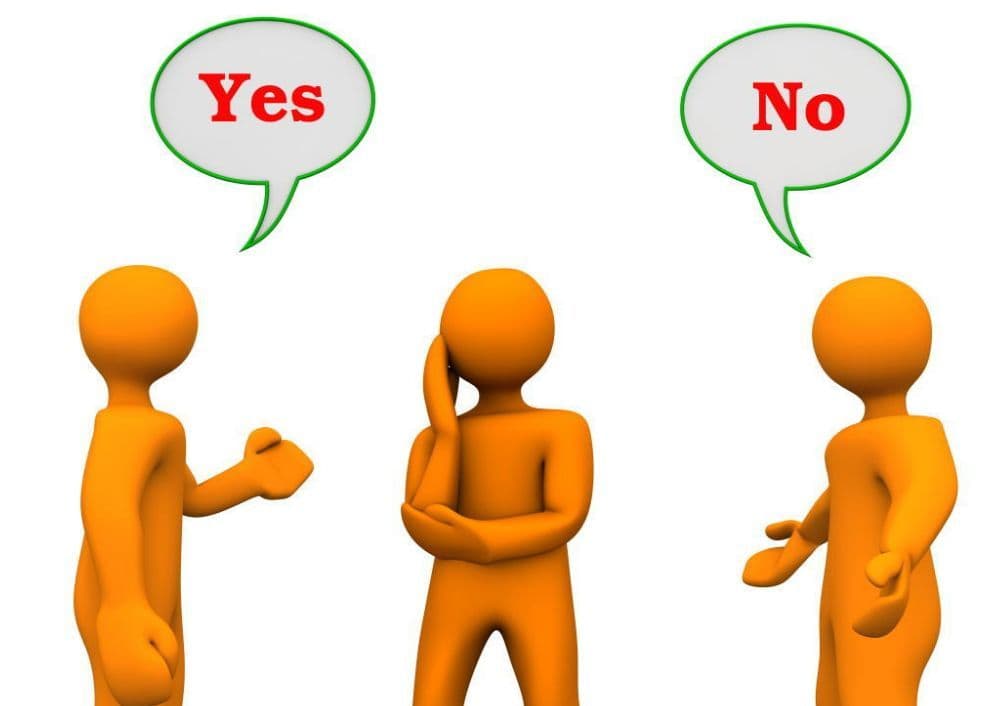
全業種向け
社内対立解消支援
どちらの意見も間違ってはいないため対立が生じている社内問題について解決に導きます。
対立解消でやってはいけないことは双方の意見を足して2で割る解決策を押し付けることです。
当社の対立解消支援は、双方が対積極的に対立解消方法を考える体制を作るところに特徴があります。
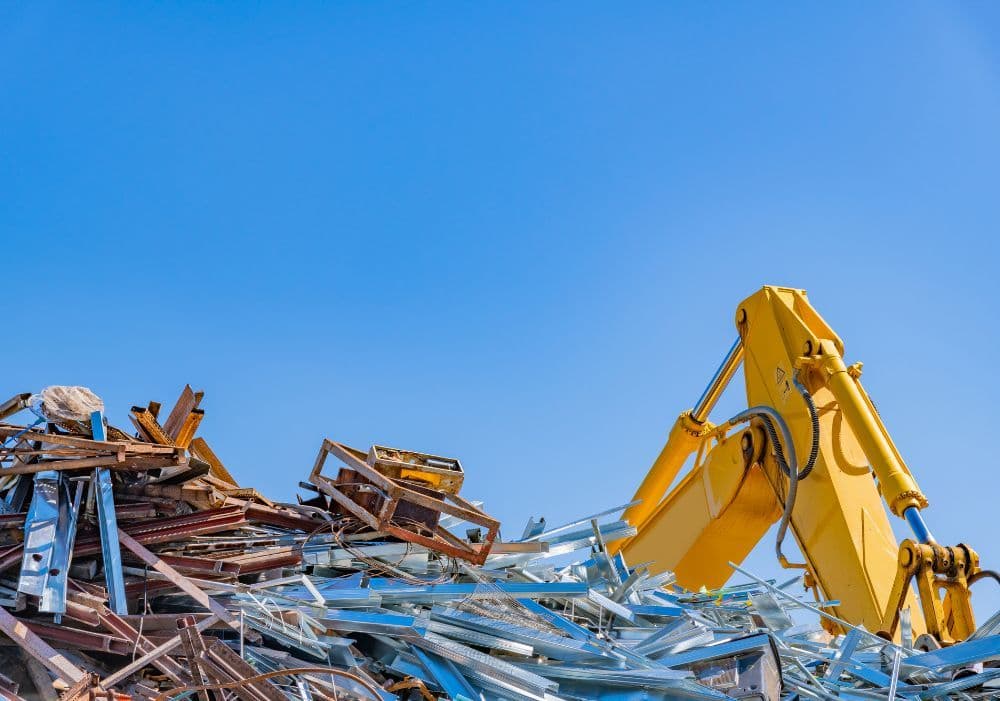
産廃業者向け
経営診断書作成
産廃処分業者および産廃収集運搬業者向けの経営診断書(財務診断書、経理的基礎を有することの説明書)を作成します。納期は通常2週間以内、最短2日です。
お客様のところへ訪問しないので全国対応可能です。
詳細は当社が運営している産廃診断特設サイト「産廃診断.jp」をご参照ください。
産廃診断.jpのサイトへジャンプするにはこちらをクリック
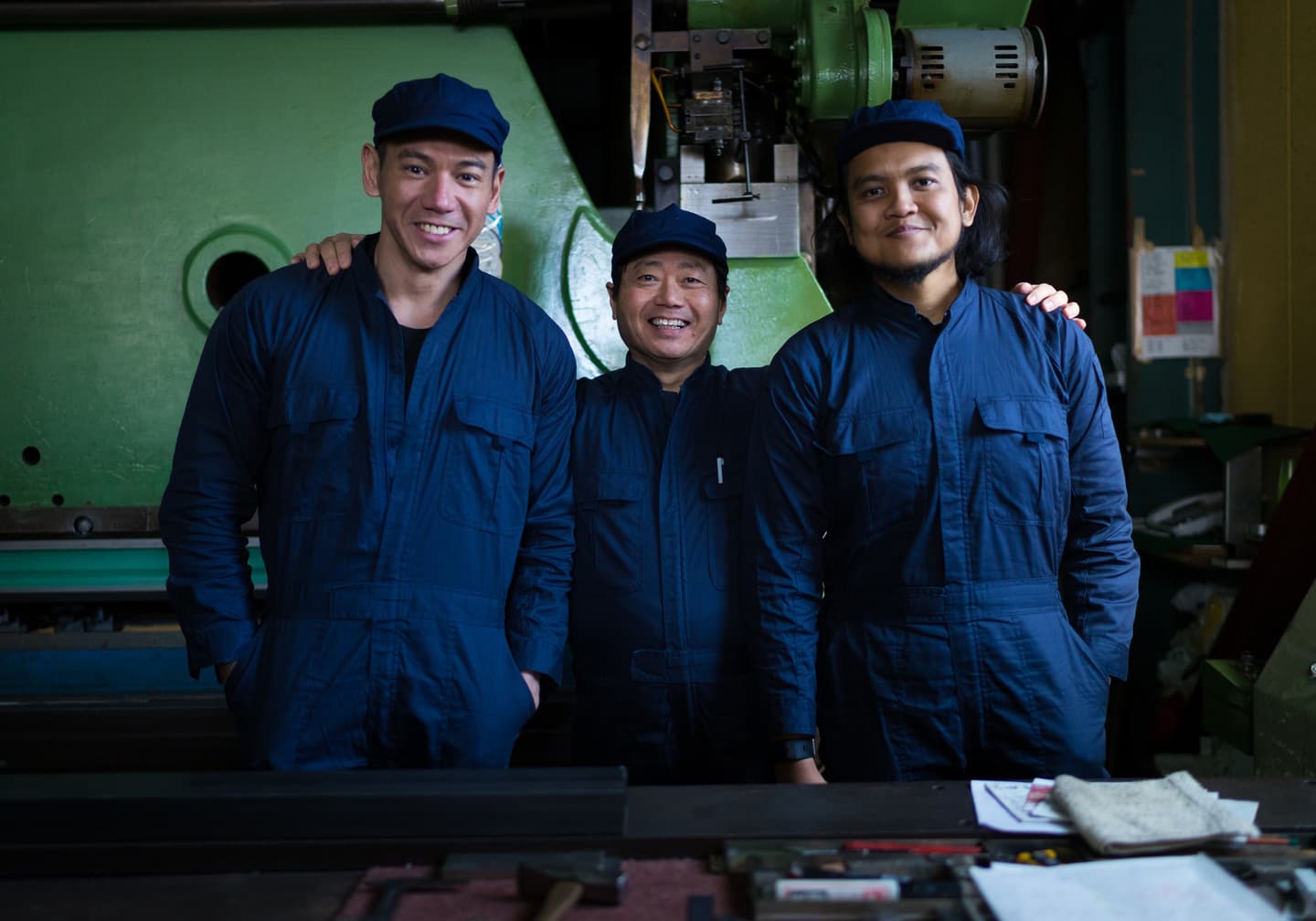
全業種向け
企業評価書作成
育成就労制度(旧:外国人技能実習生制度)を使って外国人材を受け入れる際、債務超過の企業は「外国人材の受入れに係る企業評価書」が必要となります。この企業評価書をお客様のところへ訪問せず短期間で作成します。訪問しないので全国対応可能です。
企業評価書の作成に必要となる書類は産廃業者向けの経営診断書と同じものになります。依頼方法は産廃診断特設サイト「産廃診断.jp」をご参照ください。
産廃診断.jpのサイトへジャンプするにはこちらをクリック